Frederick Winslow Taylor also known as the father of scientific management, introduced the 14 principles of scientific management by Frederick Taylor to improve workplace efficiency. These principles revolutionized traditional management methods by emphasizing systematic observation, data collection, and practical application. Taylor aimed to replace guesswork with science to achieve optimal productivity and harmony between management and workers. His approach remains a cornerstone of modern management practices and continues to guide industries in achieving higher efficiency and output.
14 Principles of Scientific Management by Frederick Taylor
Taylor’s principles serve as a detailed blueprint for organizations to maximize productivity through structured and systematic practices. Each principle focuses on a specific aspect of management, promoting efficiency and eliminating inefficiencies.
Division of Labor
Taylor’s division of labor principle emphasizes breaking down work into specialized tasks. Assigning specific duties to workers allows them to focus and build expertise in their roles.
The principle of division of labor ensures that every worker concentrates on a specific part of the process. This leads to increased efficiency, better output quality, and faster completion of tasks. Taylor believed that when workers focus on a single aspect of a job, they develop expertise, reducing errors and wastage.
- Taylor observed that when workers handle varied tasks, their performance suffers due to a lack of specialization.
- Specialization helps employees gain mastery over tasks, improving speed and accuracy.
- Example: In an automobile assembly line, one worker installs tires while another paints the body. Each task is done with precision and efficiency.
Division of labor not only improves workflow but also reduces the physical and mental strain on workers, as they focus on one task rather than multitasking.
Scientific Selection of Workers
Taylor believed that the right job should be given to the right person. He advocated for scientifically selecting workers based on their skills and aptitudes to ensure maximum efficiency.
The concept revolves around assigning roles based on an individual’s strengths. This ensures that employees can perform tasks effectively without undue stress or inefficiency. By using scientific methods like skill testing, organizations can hire and assign roles more strategically.
- Organizations should conduct skill assessments during recruitment.
- Performance evaluations can identify whether workers are suitable for their current roles or require a shift.
- Example: Hiring a graphic designer based on their portfolio and technical skill test ensures the right match for the job.
Scientific selection reduces turnover and enhances overall productivity by ensuring that workers are comfortable and capable in their roles.
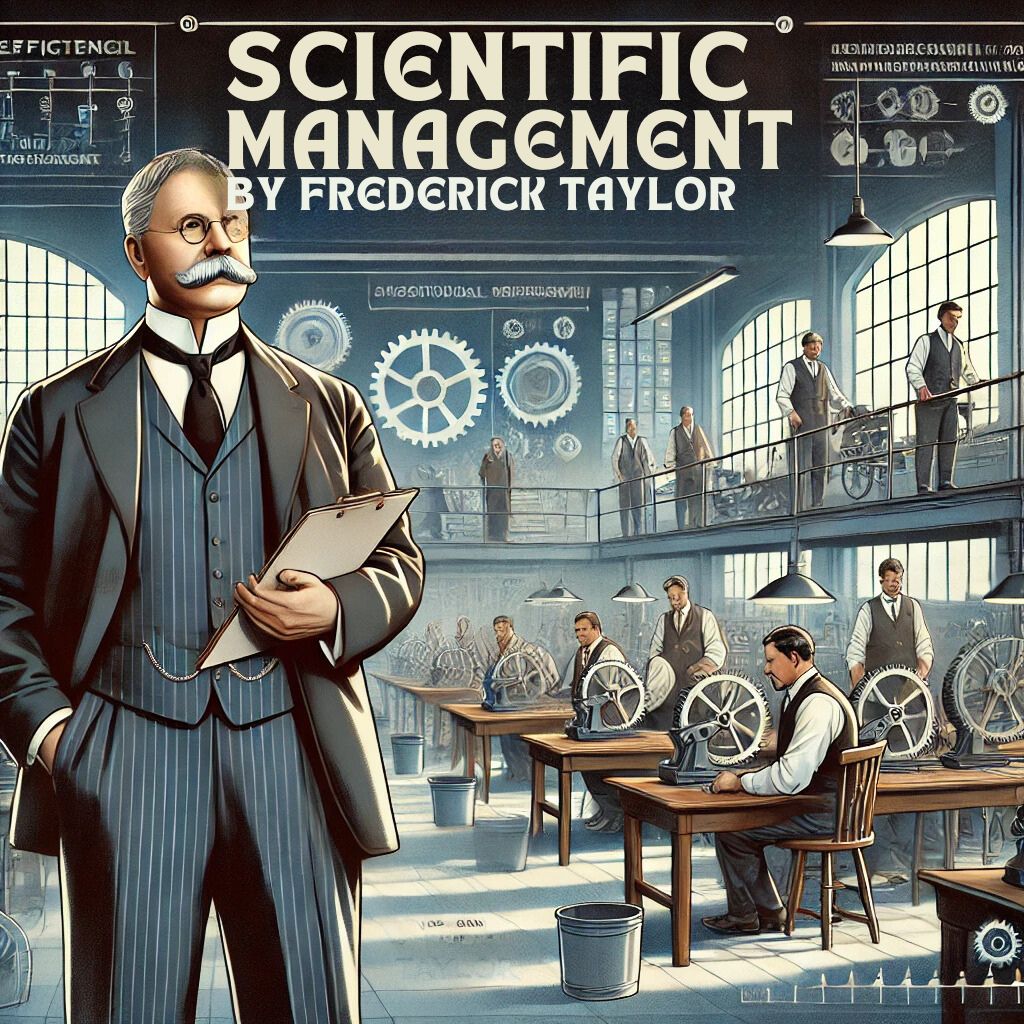
Scientific Training and Development of Workers
Training and development are key aspects of Taylor’s principles. He argued that providing systematic training equips workers with the skills required for their specific roles.
Proper training ensures that workers know the best practices for their tasks. Taylor emphasized continuous training to keep up with evolving techniques and technologies. Scientific training eliminates inefficiencies caused by trial-and-error approaches.
- Implement training programs aligned with organizational goals.
- Use step-by-step instructions to teach workers standardized methods.
- Example: A factory might provide safety training for handling hazardous materials.
Regular training enhances worker confidence, reduces mistakes, and keeps the workforce adaptable to changes.
Equal Division of Responsibility Between Management and Workers
Taylor advocated for a clear division of responsibilities between management and workers to avoid misunderstandings and conflicts.
The management should handle planning, strategizing, and organizing tasks, while workers focus on execution. This separation ensures that both parties excel in their respective domains, contributing to overall efficiency.
- Management is responsible for creating workflows and providing tools for workers.
- Workers carry out tasks as instructed, ensuring adherence to standards.
- Example: Supervisors plan resource allocation in construction projects, while laborers execute the groundwork.
Equal responsibility prevents overburdening either side and fosters mutual respect and cooperation.
Scientific Methods to Establish Performance Standards
Setting performance benchmarks based on empirical studies helps maintain consistency and productivity. Taylor emphasized the importance of realistic and measurable performance standards. These standards act as goals for workers and provide a basis for evaluating efficiency.
- Time-and-motion studies identify the most efficient ways to perform tasks.
- Benchmarks help workers and managers understand expected performance levels.
- Example: Based on empirical data, a manufacturing unit might set a standard of producing 200 units per day.
Standards help identify inefficiencies, ensuring continuous improvement in processes and output.
Scientific Methods to Plan and Control Work
Planning and controlling work systematically ensures smooth operations and resource utilization. Taylor believed that management should adopt scientific methods to plan tasks and monitor their progress. This eliminates guesswork and ensures the organization meets its objectives efficiently.
- Develop detailed project plans outlining resources, timelines, and responsibilities.
- Use performance-tracking tools to monitor progress.
- Example: Implementing Gantt charts to visualize project timelines and identify bottlenecks.
Scientific planning and control minimize delays, reduce costs, and improve overall workflow.
Harmonious Cooperation Between Management and Workers
Cooperation fosters a positive workplace culture and ensures alignment between management and workers. Taylor emphasized the importance of fostering teamwork and mutual respect between management and employees. Collaboration leads to a more cohesive and productive work environment.
- Encourage open communication to address grievances and suggestions.
- Align organizational goals with individual objectives for mutual benefit.
- Example: Holding regular meetings to discuss challenges and brainstorm solutions.
Harmonious cooperation improves morale, reduces turnover, and drives productivity.
Maximum Output at Minimum Cost
This principle focuses on achieving cost-efficiency without compromising quality. Taylor proposed that organizations should aim to maximize output by optimizing resources. Reducing wastage and streamlining processes leads to cost savings and higher profitability.
- Use automation and modern tools to enhance efficiency.
- Identify and eliminate non-value-adding activities.
- Example: Switching to energy-efficient machinery reduces electricity bills.
Maximizing output at a minimum cost ensures long-term sustainability for businesses.
Development of Workers’ Full Potential
Organizations should nurture their employees’ skills and abilities to realize their maximum potential. Taylor believed that workers thrive in environments that provide growth opportunities. Encouraging skill development benefits both the employees and the organization.
- Offer career advancement opportunities and mentorship programs.
- Conduct regular performance reviews to identify strengths and areas for improvement.
- Example: Promoting an employee who demonstrates leadership capabilities boosts morale.
Investing in employee development fosters loyalty and enhances organizational performance.
Scientific Tools and Cooperation
Taylor emphasized the importance of using scientific tools and methods to facilitate cooperation and efficiency. The right tools simplify tasks and improve precision, while teamwork ensures cohesive execution. Taylor believed in leveraging science and technology to enhance productivity.
- Equip workers with modern tools to streamline tasks.
- Foster teamwork by encouraging collaboration and mutual support.
- Example: Providing ergonomic tools in factories improves worker comfort and efficiency.
Scientific tools and teamwork create a productive and harmonious workplace.
Job Specialization
Taylor’s principle of specialization highlights the benefits of assigning specific tasks to individuals based on their skills and expertise. Specialized roles lead to mastery, allowing workers to perform tasks faster and more accurately. Specialization minimizes errors and reduces time wastage.
- Assign tasks based on employee strengths and preferences.
- Avoid overburdening workers with unrelated tasks.
- Example: In healthcare, surgeons, nurses, and anesthesiologists specialize in distinct roles.
Job specialization enhances efficiency and ensures high-quality output.
Clear and Fair Wage System
A transparent and equitable wage system motivates workers to perform at their best. Taylor believed that fair compensation tied to performance creates a motivated workforce. Clear wage policies eliminate disputes and promote trust.
- Introduce performance-based bonuses and incentives.
- Ensure wages are competitive and meet industry standards.
- Example: Offering bonuses for meeting production targets boosts morale.
A fair wage system attracts and retains talent while enhancing productivity.
Discarding Traditional Practices
Taylor strongly opposed outdated and unscientific methods, advocating for continuous innovation. Organizations must adopt modern practices to stay competitive. Taylor emphasized the importance of analyzing and updating processes regularly.
- Regularly review and refine workflows to eliminate inefficiencies.
- Adopt new technologies and methodologies.
- Example: Replacing paper-based record-keeping with digital systems increases accuracy and speed.
Discarding traditional practices ensures organizations remain adaptable and forward-thinking.
Development of a Science for Each Element of Work
This principle focuses on using scientific analysis to optimize every aspect of work. Taylor proposed studying each task to identify the most efficient methods and documenting these findings for consistent application.
- Use data and experiments to determine optimal practices.
- Train workers to implement these methods accurately.
- Example: Conducting time-and-motion studies to streamline assembly line operations.
Scientific work analysis ensures precision, consistency, and efficiency.
Principles of Scientific Management FAQs
What is the goal of the 14 principles of scientific management by Frederick Taylor?
The goal is to enhance productivity and efficiency through systematic, scientific methods while fostering harmony between management and workers.
How does job specialization improve efficiency?
Job specialization focuses on assigning tasks based on individual strengths, leading to faster, more accurate work with minimal errors.
Why is scientific selection of workers important?
It ensures the right person is matched to the right job, enhancing performance and reducing turnover.
What role does harmonious cooperation play in Taylor’s principles?
Harmonious cooperation improves workplace morale, aligns goals, and fosters a collaborative environment.
Why should traditional practices be discarded?
Discarding outdated methods allows organizations to adopt innovative techniques, ensuring competitiveness and adaptability.