One of the most important factors in managing a business is the analysis of production and cost. With help of cost and production analysis, organizations can make effective decisions regarding competitive pricing, the right level of production, and cost efficiency. In a very real sense this also means that when a company looks at its production costs, it is in such an embryo because different factors lie behind the production cost, such as certain relationships and some statistical results. Furthermore, the operation of the management of the cost covers the concept of opportunity costs. Worthy mentioning is other popular important concepts in cost and production analysis including cost classification, production function, cost curves, and so on.
What is Production and Cost Analysis?
Production and cost analysis mainly reflect the assessment of resource utilization in producing goods or services. Of course, they also take into consideration costs related to such processes. It deals with the study of relationships involving input factors like labor, capital, and raw materials in relation to what comes out in the form of products. Production and cost analysis enable avoiding unnecessary costs when maximizing production efficiency. Such analysis is a significant parameter within which businesses can adopt an exit pricing strategy and plan for their expenses. Such production and cost analysis will help in passing informed judgments on increasing scales of operation.
Types of Costs in Production
In any production environment, costs can be broadly divided into fixed costs, variable costs, and semi-variable costs. Each type of cost behaves differently as production levels change, which has significant implications for pricing and profitability.
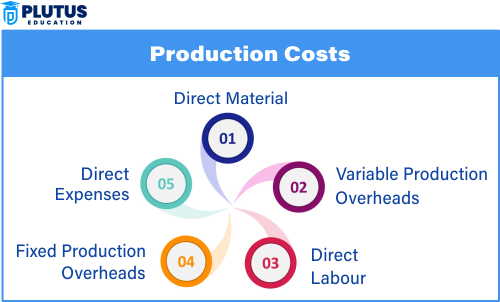
Fixed Costs
- Definition: Fixed costs are expenses that remain constant, regardless of the level of production. These costs do not change whether the company produces a few units or a large volume.
- Examples: Rent, salaries of permanent staff, insurance premiums, and depreciation of equipment.
- Key Impact: Fixed costs contribute to the overhead of the business and must be covered even if production is minimal. Businesses with high fixed costs need to produce at higher volumes to spread these costs and ensure profitability.
Variable Costs
- Definition: Variable costs are expenses that change in direct proportion to the volume of production. As the number of units produced increases, the variable costs also rise.
- Examples: Raw materials, labor costs for temporary workers, utility costs based on production levels, and packaging.
- Key Impact: Variable costs are crucial to understanding profitability at different levels of output. As production scales up, variable costs increase, but they also contribute to the overall revenue generated from sales.
Semi-variable Costs
- Definition: Semi-variable costs have characteristics of both fixed and variable costs. These costs remain fixed to some extent but can change when production exceeds a certain level.
- Examples: Electricity bills that remain constant but increase with the intensity of production, or telephone bills with a fixed monthly charge plus extra charges for increased usage.
- Key Impact: Businesses need to track semi-variable costs closely to anticipate when they will transition from fixed to variable behavior, as this can influence cost predictions and pricing strategies.
The Production Function Explained
The production function is a fundamental concept in production and cost analysis. It illustrates the relationship between the quantity of inputs used in production and the resulting output. It shows how varying levels of input resources (like labor, capital, and raw materials) can influence the output produced by a business.
Short-Run vs. Long-Run Production Functions
- Short-Run Production Function: In the short run, at least one factor of production (e.g., capital or machinery) is fixed. Firms can only adjust the amount of variable factors (e.g., labor or raw materials) to increase production. The production function reflects this limitation.
- Long-Run Production Function: In the long run, firms can adjust all factors of production. There are no fixed costs, allowing businesses to optimize all inputs for the best possible output.
Short-Run vs. Long-Run Production Functions
Feature | Short-Run Production Function | Long-Run Production Function |
Time Frame | Short period where at least one input is fixed | Long period where all inputs are variable |
Inputs | One or more inputs (usually capital) are fixed | All factors of production can be changed |
Flexibility | Limited flexibility in adjusting input combinations | Full flexibility in changing scale and combinations |
Cost Types Involved | Involves both fixed and variable costs | Only variable costs exist |
Returns | Subject to Law of Variable Proportions | Subject to Returns to Scale |
Purpose | Analyzes output when adding more of a variable input | Analyzes output when changing all inputs proportionally |
Examples | Adding more workers to a factory with fixed machines | Expanding the entire factory with more machines and workers |
Time Horizon | Typically weeks or months | Typically years |
Graphical Representation | Total Product, Marginal Product, Average Product curves | Isoquants and Isocost curves |
Scalability | Cannot scale fully due to fixed factors | Can scale up or down fully |
Inputs and Outputs
The production function shows the level of output that can be achieved for each combination of inputs. For instance, a factory might use a set number of workers and machines (inputs) to produce a certain quantity of goods (output). The goal is to determine the most efficient use of resources that maximizes output while minimizing costs.
- Increasing Returns to Scale: When an increase in inputs leads to a more than proportional increase in output.
- Constant Returns to Scale: When an increase in inputs leads to a proportional increase in output.
- Decreasing Returns to Scale: When increasing inputs results in less than proportional increases in output.
The Law of Diminishing Returns
The Law of Diminishing Returns is a key concept in production theory, stating that as more units of a variable input (e.g., labor) are added to fixed inputs (e.g., machinery or land), the additional output produced by each new unit of input will eventually decrease.
- Decreased Efficiency: As production continues, workers may become overcrowded or machinery may become overused, leading to lower productivity per unit of input.
- Cost Implications: Diminishing returns can increase marginal costs because additional inputs are less effective at increasing output. This phenomenon can lead to higher unit costs and reduced profitability at higher levels of production.
Understanding Cost Curves
Costs and output are related to each other graphically. Cost plots can show how the different cost types behave for every level of shift in production.
Total Cost Curve
This is total cost curve by which total cost incurred over the quantity of output produced is expressed. It gives the total fixed and variable costs involved at a certain level of production.
- Shape: Usually by relating an upward slope in the short-run total cost curve, the total cost is indicating that more costs should increase as some more units may be produced.
- Significance: Businesses may derive the total cost curve to forecast and predict the costs’ increase with increased production quantities as well as defining levels of production.
Marginal Cost Curve
The additional cost of producing one more unit is termed as the marginal cost curve produced. Thus, the marginal cost curve defines how much the total cost changes with the increase in production.
- Shape: Since diminishing returns are reflected in this U-shape nature of marginal cost example, marginal initially employs decrease in cost due to a more efficient production; however, they increase over time due to diminishing returns.
- Importance: To pricing decisions, marginal cost becomes crucial. It would be necessary for a company to set prices at least equal to marginal cost to prevent losses and ensure profitability.
Average Cost Curve
In terms of output, average cost refers to the cost incurred per unit produced. Average costs are calculated as number of units produced into total cost consumed producing units.
- Shape: Like a marginal cost curve, average costs are usually shaped like a U. With increased production, they decrease at first, but thereafter increase with more production as a result of diminishing returns.
Factors Affecting Production and Cost
There are many factors affecting the level of production and subsequently the costs incurred. Considering these factors will enable businesses to make sound decisions about improving efficiency and profitability.
- Advancements in Technology: An improved technology enhances production in terms of better resource efficiencies as well as increased productivity. In addition, it entailed less labor costs, material waste, and cost of production.
- Labor Costs and Productivity: Labor costs, which constitute wages along with benefits and training, make a significant portion of production costs. Therefore, efficient labor management and productivity can bring costs down while increasing output.
- Cost of Raw Materials: Changing price of raw materials influences production cost. Affordable raw materials readily available enable low-cost production while making the profit margin over that extent beneficially influence the price of products.
Production and Cost Analysis FAQs
1. What is the difference between fixed cost and variable cost?
Fixed costs remain constant regardless of the level of production (e.g., rent, salaries). Variable costs change in direct proportion to the quantity of output produced (e.g., raw materials, direct labor).
2. What is the law of diminishing returns in production?
The law states that as additional units of a variable input (like labor) are added to a fixed input (like land), the marginal product of the variable input eventually declines. This concept helps firms understand optimal input levels.
3. What is marginal cost and how is it calculated?
Marginal cost is the additional cost incurred by producing one more unit of output. It is calculated as the change in total cost divided by the change in quantity produced (MC = ΔTC / ΔQ).
4. Why does the marginal cost curve initially fall and then rise?
Initially, marginal cost falls due to increasing marginal returns, but it eventually rises because of diminishing marginal returns. This U-shape reflects the efficiency and inefficiency of resource use at different output levels.
5. How is average cost different from marginal cost?
Average cost is the total cost per unit of output (AC = TC/Q), while marginal cost measures the cost of producing one additional unit. Marginal cost influences the average cost—when MC is less than AC, AC falls, and when MC is greater, AC rises.